The company has always emphasized product development and design. With the expertise of its technical team and the use of advanced steel structure design and detailing software such as PKPM, STAAD
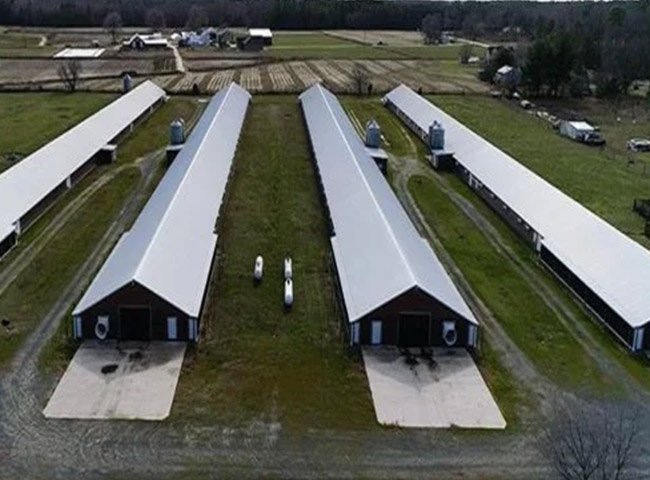
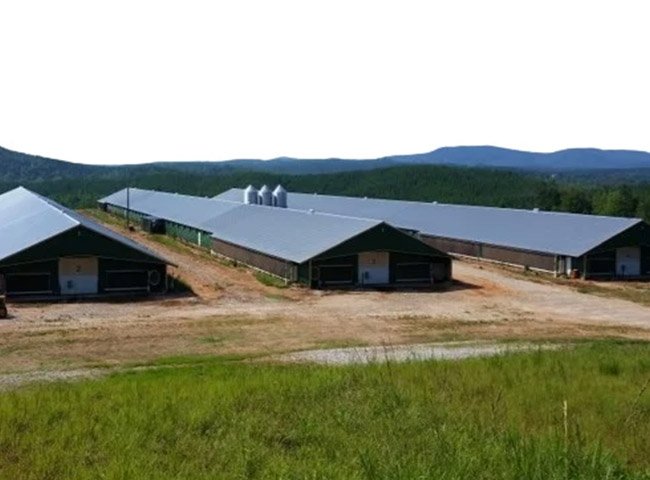
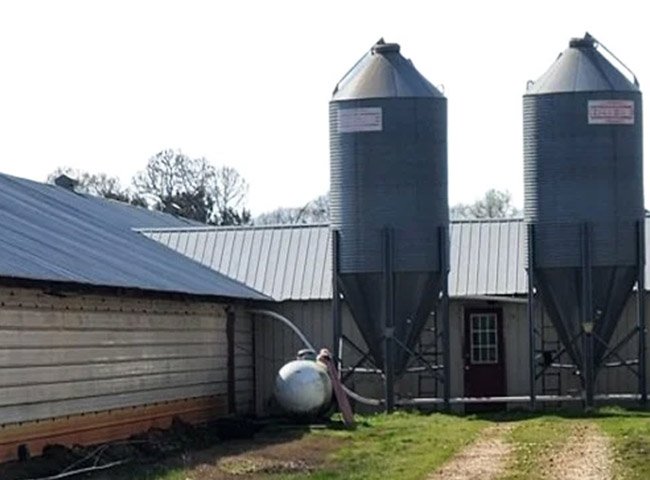

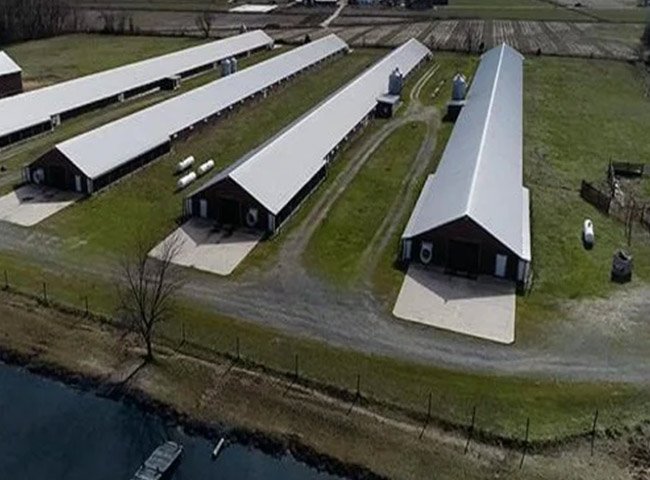
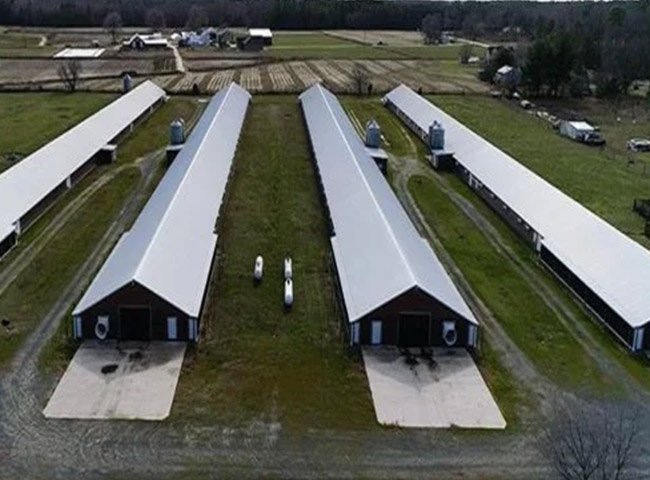
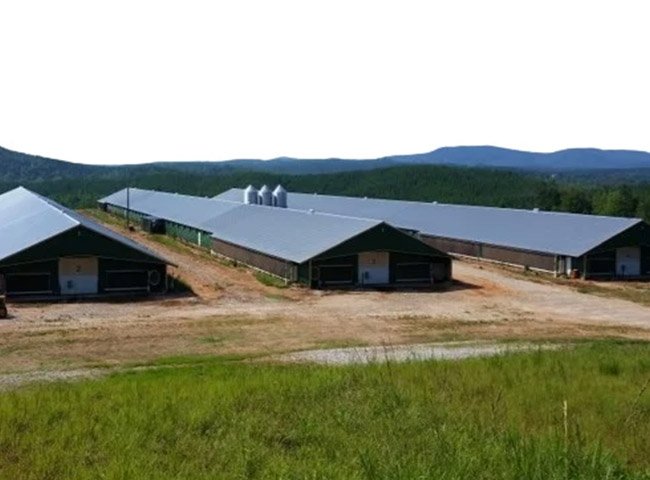
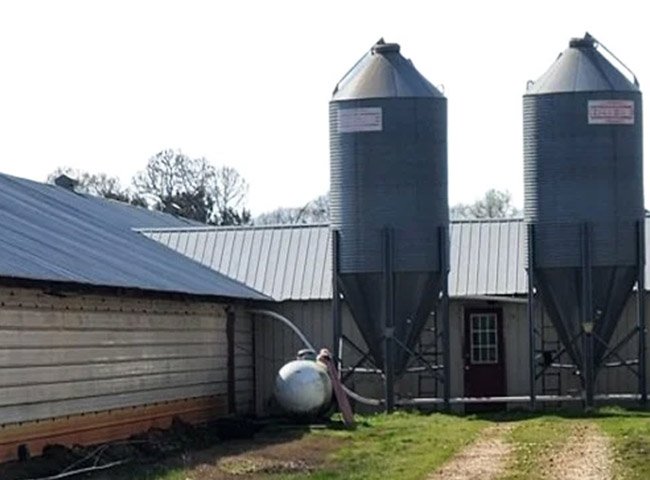

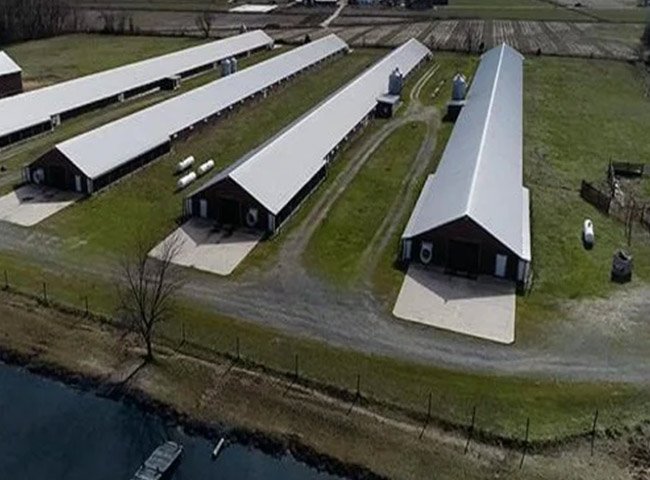
Steel Structure Building Design Chicken Poultry Farm for Sale
Custom - made Prefabricated Steel Structure Chicken House - Meeting the Needs of Modern Poultry Farming
Frame Steel
The main frame selects Q345 hot - dip galvanized steel with a yield strength of ≥ 345MPa and a tensile strength of 470 - 630MPa. After hot - dip galvanizing treatment, it has good rust - proof and corrosion - resistant properties, effectively coping with the complex environment of humidity and high ammonia in the chicken house, and ensuring the long - term stable use of the chicken house.
The secondary frame adopts Q235 galvanized square tubes, which are cost - controllable and structurally stable, providing reliable support for the overall chicken house and meeting the structural requirements of poultry - farming buildings.
Product Details
Connection Components
All connection components are made of stainless - steel materials, which have good corrosion resistance and can prevent rusting and damage in the chicken - house environment. A combination of high - strength self - tapping screws and special connection components is used, which is easy and quick to install, ensures the firmness of the structural connection, and is convenient for later maintenance and modification.
Enclosure Panels
Wall System
Outer layer: 0.5mm - thick colored aluminized zinc profiled steel sheet with an aluminized zinc content of 180g/㎡. It has excellent corrosion - prevention ability, can resist the erosion of rainwater and humid air, has long - lasting colors, and can be selected in appropriate colors to blend with the surrounding environment.
Insulation layer: 50 - 100mm - thick polyurethane sandwich panel with a thermal conductivity of ≤ 0.025W/(m·K). It has excellent heat - insulation and heat - preservation performance, effectively maintaining a stable temperature in the chicken house, reducing energy consumption, and providing a comfortable growth environment for the chicken flock.
Inner layer: 0.4mm - thick food - grade antibacterial color steel sheet with a smooth surface, which is easy to clean and disinfect, and has antibacterial functions, effectively inhibiting the growth of bacteria and ensuring the health of the chicken flock.
Roof System
Panel: 0.6mm - thick aluminized zinc color steel sheet. The special wave - shaped profiled design enhances the drainage capacity of the roof, avoids water accumulation from damaging the roof, and the aluminized zinc layer effectively extends the service life of the roof.
Insulation layer: 80mm - thick glass wool felt is used, with a thermal conductivity of ≤ 0.04W/(m·K). It can not only insulate heat but also play a certain sound - absorbing role, reducing the impact of external noise on the chicken flock.
Waterproof layer: Polymer waterproof membrane is used, which has good flexibility, weather resistance, and waterproof performance, ensuring that the roof does not leak during long - term use.
Dimension Specifications
Span: A variety of standard spans from 8 to 20 meters are provided, which can be flexibly customized according to the breeding scale and site conditions to meet the needs of equipment placement and chicken - flock activity space under different breeding modes.
Length: There is no fixed limit and can be customized according to the actual length of the site to adapt to different - shaped and sized breeding sites.
Height: The eave height ranges from 3 to 5 meters and can be adjusted according to the height of the breeding equipment and ventilation requirements to ensure that there is enough space for ventilation and equipment installation inside the chicken house.
Environmental Control Performance
Temperature control: Through the design of heat - insulation panels and a reasonable ventilation system, the temperature in the chicken house can be effectively maintained within an appropriate range. In summer, it can be cooled by a combination of natural ventilation and mechanical ventilation, and in winter, heat loss can be reduced by using heat - insulation materials.
Ventilation performance: Professional ventilation equipment such as exhaust fans and ventilation openings is equipped, and the ventilation volume can be adjusted according to the number of chicken flocks and seasons to ensure fresh air in the chicken house and keep the concentrations of harmful gases such as ammonia and hydrogen sulfide within a safe range.
Lighting system: Natural lighting windows and artificial lighting equipment can be installed. The natural lighting windows use high - light - transmittance PC sunlight panels, which can not only ensure sufficient lighting but also prevent birds from entering. Artificial lighting can be controlled regularly according to the growth stages of the chicken flock to meet the lighting needs of the chicken flock.
Internal Facility Configuration
Chicken cage system: Different - sized chicken cages can be customized according to customer needs, including stacked and stepped types. They are made of hot - dip galvanized steel wire, which is corrosion - resistant and has high strength, providing a comfortable living space for the chicken flock.
Feeding system: Automated feeding equipment such as feed lines and feed towers is equipped, which can achieve accurate feeding, reduce feed waste, and improve breeding efficiency.
Drinking - water system: Nipple - type water dispensers are used to ensure clean and hygienic water sources, save water, and at the same time effectively prevent the chicken flock from being infected with diseases.
Manure - cleaning system: Manure - cleaning methods such as scraper - type and conveyor - belt - type can be selected. They have a high degree of automation and good cleaning effects, and can promptly clean the manure in the chicken house to keep the chicken house clean.
Installation and Service
Prefabricated production: All components are prefabricated in the factory with high precision and stable quality, reducing on - site construction time and pollution to the breeding site.
Installation cycle: Depending on the size of the chicken house, the installation cycle of a 1000 - 5000㎡ chicken house is generally 10 - 25 days. It is installed by a professional installation team to ensure installation quality and construction safety.
After - sales service: Provide a 3 - year structural quality guarantee, a 1 - year enclosure - system quality guarantee, lifetime maintenance consultation services, and respond to after - sales needs within 24 hours. Timely solve the problems encountered by customers during use and ensure the long - term stable operation of the chicken house.